ASTM A105 Chemical Composition and Mechanical Properties
ASTM A105 specifies the chemical composition and mechanical properties of ASTM A105.
ASTM A105-21 covers forged carbon steel piping components including flanges, fittings and valves for ambient and higher-temperature service in pressure systems. including flanges, fittings and valves, etc. Materials shall be subjected to heat treatment (annealing, normalizing, tempering, or quenching).
Application: General non-corrosive service, -20°F(-29ºC) to 800°(425ºC)
Casting Equivalent: ASTM A216 WCB
ASTM A105 Chemical Composition
Note 1—For each reduction of 0.01 % below the specified carbon maxinnim (0.35 %), an increase of 0.06 % manganese above the specified maximum (1.05 %) will be permitted up to a maximum of 1.65 %.
Element | Composition, % |
Carbon | 0.35 max |
Manganese | 0.60-1.05 |
Phosphorus | 0.035 max |
Sulfur | 0.040 max |
Silicon | 0.10-0.35 |
Copper | 0.40 maxA |
Nickel | 0.40 maxA |
Chromium | 0.30 maxA,B |
Molybdenum | 0.12 maxA,8 |
Vanadium | 0.08 max |
A The sum of copper, nickel, chromium, molybdenum and vanadium shall not exceed 1.00 %.
B The sum of chromium and molybdenum shall not exceed 0.32 %.
ASTM A105 Mechanical PropertiesA
Tensile strength, min, ksi [MPa] | 70[485] |
Yield strength, min, ksi [MPa]s Elongation in 2 in. or 50 mm, min, %: | 36[250] |
Basic minimum elongation for walls Vie in. (7.9 mm] and over in thickness, strip tests. | 30 |
When standard round 2-in. or 50-mm gauge length or smaller proportionally sized specimen with the gauge length equal to 4D is used | 22 |
For strip tests, a deduction for each 1/32-in. [0.8-mm] decrease in wall thickness below in. [7.9 mm] from the basic minimum elongation of the percentage points of Table 3 | 1.50c |
Reduction of area, min, %° | 30 |
Hardness, HBW, max | 197 |
A For small forgings, see 8.3.4.
B Determined by either the 0.2 % offset method or the 0.5 % extension-under-load method.
C See Table 3 for computed minimum values.
D For round specimens only.
Hardness:
The hardness of all forgings so tested shall be 137 to 197 HBW inclusive.
ASTM A105 -21 Specifications
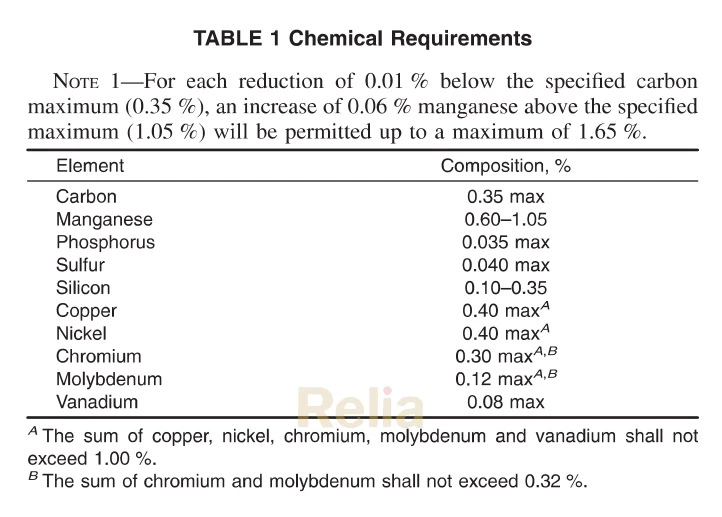
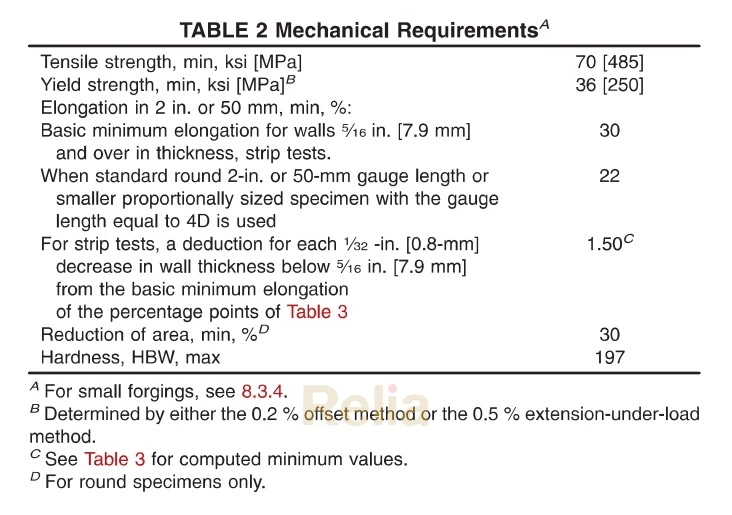
8.4 Hardness Tests:
8.4.1 Two hardness tests shall be made for each heat of as-forged components. When more than one forging is produced from each heat, a minimum of two forgings shall be tested with one reading from each forging. When only one forging is produced, it shall be tested in two locations.
8.4.2 Except when only one forging is produced, a minimum of two forgings shall be hardness tested per batch or continuous run as defined in 832.2 to ensure that forgings are within the hardness limits given in Table 2. When only one forging is produced, it shall be hardness tested in two locations to ensure it is within the hardness limits given in Table 2.
8.4.3 Testing shall be as specified in Specification A961/ A961M. The purchaser may verify that the requirement has been met by testing at any location on the forging, provided such testing does not render the forging useless.
A105 Working Pressure Temperature Rating (ASME B16.34)
Standard Class
Temperaiure,℃ | Working Pressures by Class, bar | ||||||
150 | 300 | 600 | 900 | 1500 | 2500 | 4500 | |
-29 to 38 | 19.6 | 51.1 | 102.1 | 153.2 | 255.3 | 425.5 | 765.9 |
50 | 19.2 | 50.1 | 100.2 | 150.4 | 250.6 | 417.7 | 751.9 |
100 | 17.7 | 46.6 | 93.2 | 139.8 | 233.0 | 388.3 | 699.0 |
150 | 15.8 | 45.1 | 90.2 | 135.2 | 225.4 | 375.6 | 676.1 |
200 | 13.8 | 43.8 | 87.6 | 131.4 | 219.0 | 365.0 | 657.0 |
250 | 12.1 | 41.9 | 83.9 | 125.8 | 209.7 | 349.5 | 629.1 |
300 | 10.2 | 39.8 | 79.6 | 119.5 | 199.1 | 331.8 | 597.3 |
325 | 9.3 | 38.7 | 77.4 | 116.1 | 193.6 | 322.6 | 580.7 |
350 | 8.4 | 37.6 | 75.1 | 112.7 | 187.8 | 313.0 | 563.5 |
375 | 7.4 | 36.4 | 72.7 | 109.1 | 181.8 | 303.1 | 545.5 |
400 | 6.5 | 34.7 | 69.4 | 104.2 | 173.6 | 289.3 | S20.8 |
425 | 5.5 | 28.8 | 57.5 | 86.3 | 143.8 | 239.7 | 431.5 |
450 | 4.6 | 23.0 | 46.0 | 69.0 | 115.0 | 191.7 | 345.1 |
475 | 3.7 | 17.4 | 34.9 | 52.3 | 87.2 | 145.3 | 261.5 |
500 | 2.8 | 11.8 | 23.5 | 35.3 | 58.8 | 97.9 | 176.3 |
538 | 1.4 | 5.9 | 11.8 | 17.7 | 29.5 | 49.2 | 88.6 |
NOTES:
- Upon prolonged exposure to temperatures above 425°C, the carbide phase of steel may be converted to graphite. Permissible, but not recommended for prolonged usage above 425°C.
- Only killed steel shall be used above 455°C.
- Not to be used over 370°C.
- Not to be used over 455°C.
- Not to be used over 260°C.
- Not to be used over 345°C.